
It is generally equipped with probes that, with the use of instruments, can measure intake temperature and pressure (total and static). The amount of change in duct area and the magnitude of the shock are varied automatically with the airspeed of the aircraft.Ī bellmouth inlet is usually installed on an engine undergoing testing in a test cell. The same device that changes the area of the duct also sets up a shock wave that further reduces the speed of the incoming air within the duct. In at least one aircraft installation, both the shock method and the variable-geometry method of causing diffusion are used in combination. The shock wave results in diffusion of the airflow, which, in turn, decreases the velocity of the airflow. A shock wave is willfully set up in the supersonic flow of the air entering the duct, by means of some restriction or small obstruction which automatically protrudes into the duct at high flight Mach numbers. Stronger shock waves produce larger changes in the properties of the air or gas. A shock wave is a thin region of discontinuity in a flow of air or gas, during which the speed, pressure, density, and temperature of the air or gas undergo a sudden change. The third method is the use of a shock wave in the airstream.
#Pure silver aircraft inklet series#
A series of turning vanes is sometimes placed in the side-scoop inlet to assist in straightening the incoming airflow and to prevent turbulence. These side scoops are placed as far forward as possible to permit a gradual bend toward the compressor inlet, making the airflow characteristics approach those of a single-entrance duct. Scoops at the sides of the fuselage are often used. Internally, the problem is the same as that encountered with the single-entrance duct: to construct a duct of reasonable length with as few bends as possible.
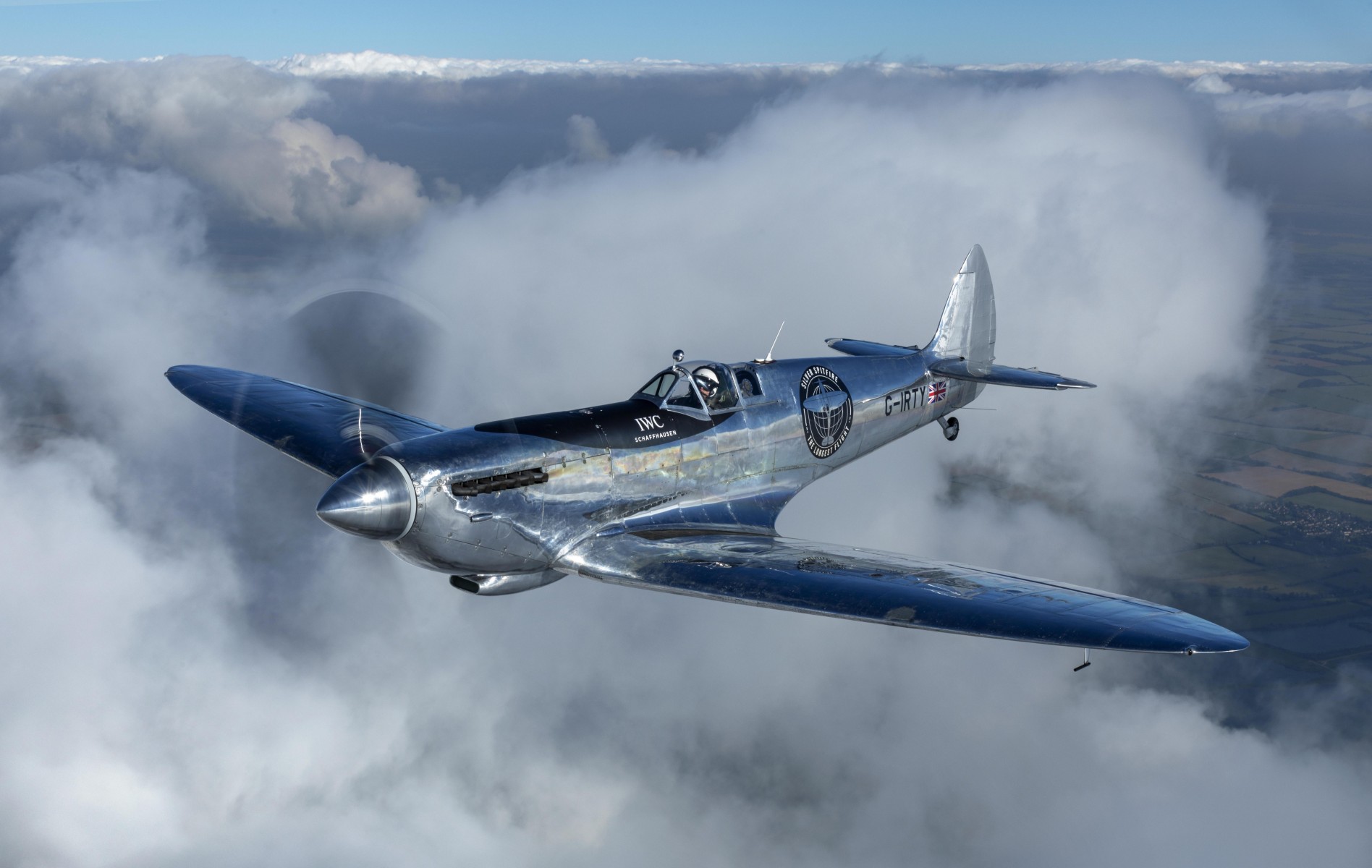
Either type of duct presents more problems to the aircraft designer than a single-entrance duct because of the difficulty of obtaining sufficient airscoop area without imposing prohibitive amounts of drag. This divided duct can be either a wing-root inlet or a scoop at each side of the fuselage. Some form of a divided duct, which takes air from either side of the fuselage, has become fairly widely used. The requirements of high-speed, single- or twin-engine military aircraft, in which the pilot sits low in the fuselage and close to the nose, render it difficult to employ the older type single-entrance duct, which is not used on modern aircraft. The choice of configuration of the entrance to the duct is dictated by the location of the engine within the aircraft and the airspeed, altitude, and attitude at which the aircraft is designed to operate. On turbofan engines, the duct must have a sufficiently straight section to ensure smooth, even airflow because of the high airflows. On engines with low flow rates, turning the airflow allows the engine nacelle to be smaller and have less drag.
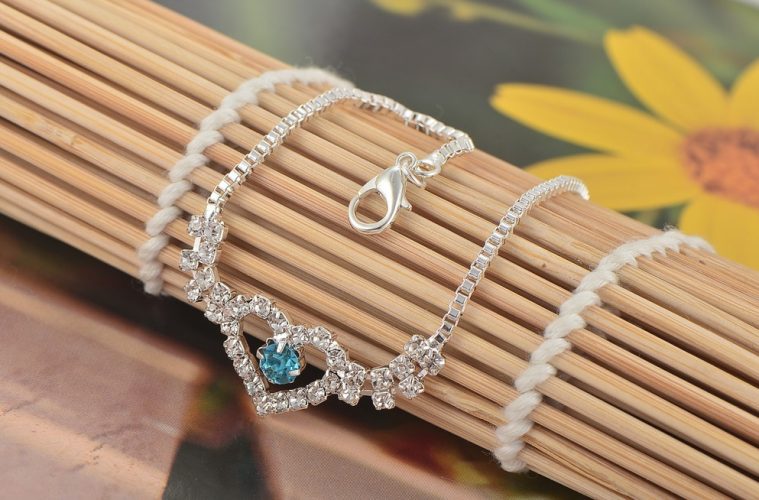
Smooth flow depends upon keeping the amount of turbulence to a minimum as the air enters the duct. The engine inlet duct must also hold the drag effect on the aircraft to a minimum.Īir pressure drop in the engine inlet is caused by the friction of the air along both sides of the duct and by the bends in the duct system. This is known as “ram recovery” or “total pressure recovery.” The inlet duct must uniformly deliver air to the compressor inlet with as little turbulence and pressure variation as possible. This added pressure at the inlet of the engine increases the pressure and airflow to the engine. As air molecules are trapped and begin to be compressed in the inlet, much of the pressure loss is recovered.
#Pure silver aircraft inklet free#
The inlet must be able to recover as much of the total pressure of the free airstream as possible. As aircraft speed increases, thrust tends to decrease somewhat as the aircraft speed reaches a certain point, ram recovery compensates for the losses caused by the increases in speed.
